Shit Happens (part 3)
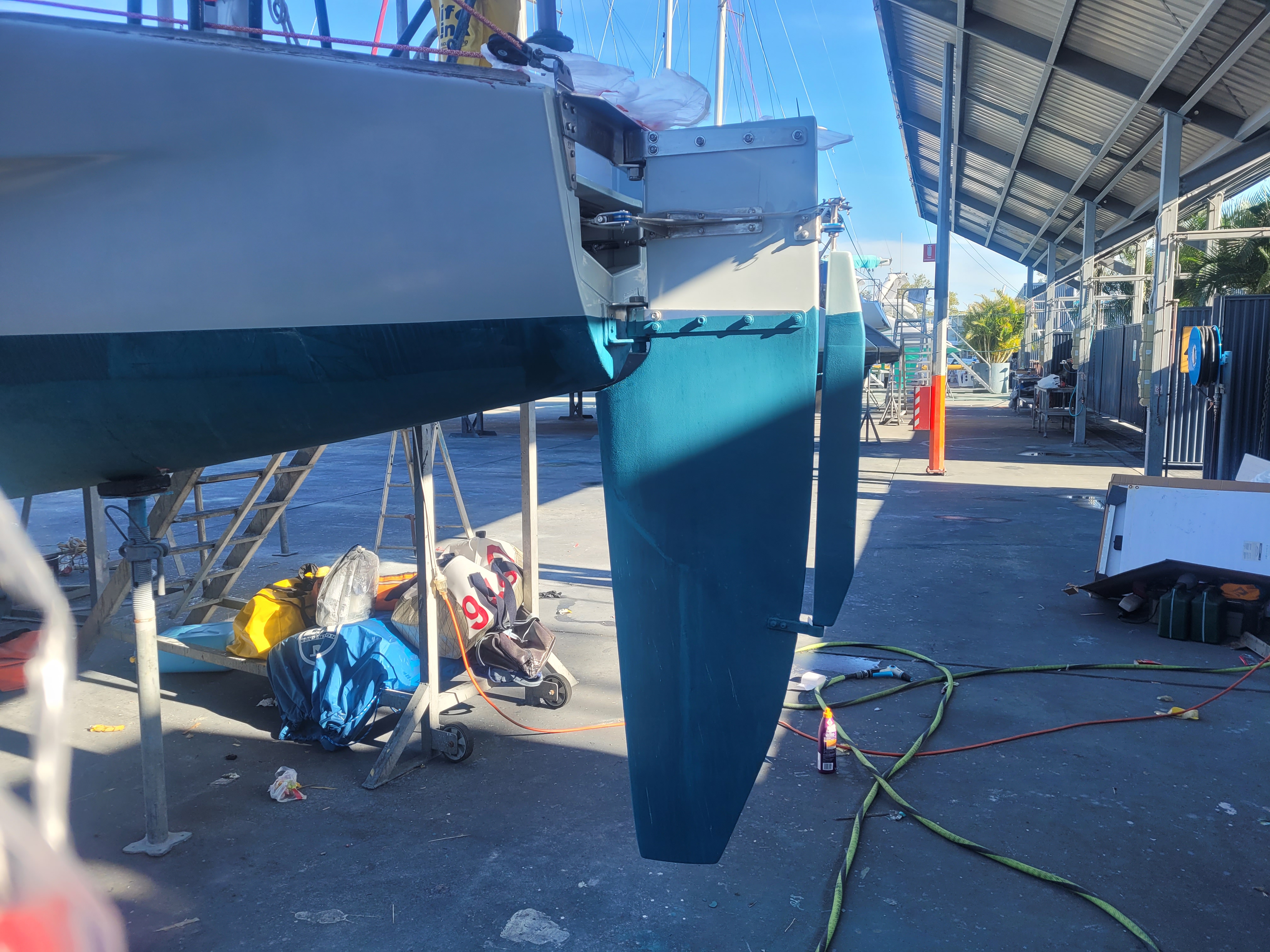
In part 1, we looked at the rudder breakage and the tale of returning to Australia under rescue tow. In part 2, we took a closer look at exactly what happened based on available evidence. In part 3, I want to get into the repair process and how things came back together.
Redesigning the Rudder Mounts
One of the first people I emailed after getting a closer look at what failed in the rudder was a well-known Condor 40 owner, who also looped in the boat's designer. The designer provided some plans for a later-model rudder update for the Condor 40, and I used that design to discuss ideas with a local metal fabrication shop.
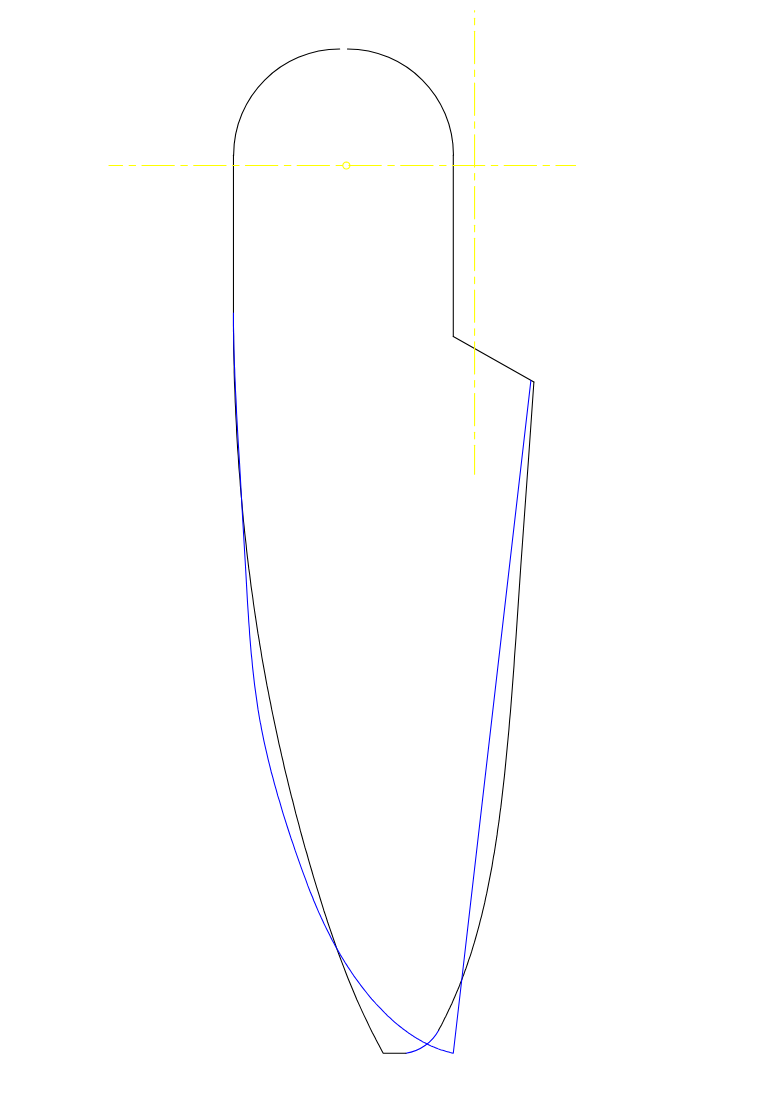
The main problem (see part 2 for more) was old, bad steel in the rudder cage. But the updated design also added a bit more lateral structure in the rudder cage sections where load is transferred to the pintles. In the spirit of overbuilding the critical components during this rebuild, while keeping the rudder weight and balance similar to the original, we made the following changes when re-designing how the rudder mounts:
1) Change from a kick-up cage to a fixed, two-pintle design
The original rudder cage was designed with multiple smaller "sacrificial" bolts and a larger, central bolt. This design allows the rudder to "kick up" if it experiences a grounding hard enough to sheer off the smaller bolts. This is a nice feature, but introduces complexity and requires a large, fully surrounding cage.
For simplicity, the new design uses a basic "two bar" structure rather than a full cage. This should allow sufficient surface area for the loads to be distributed on the rudder, with multiple bolts strong enough to hold the assembly together. It also saves a significant amount of weight.
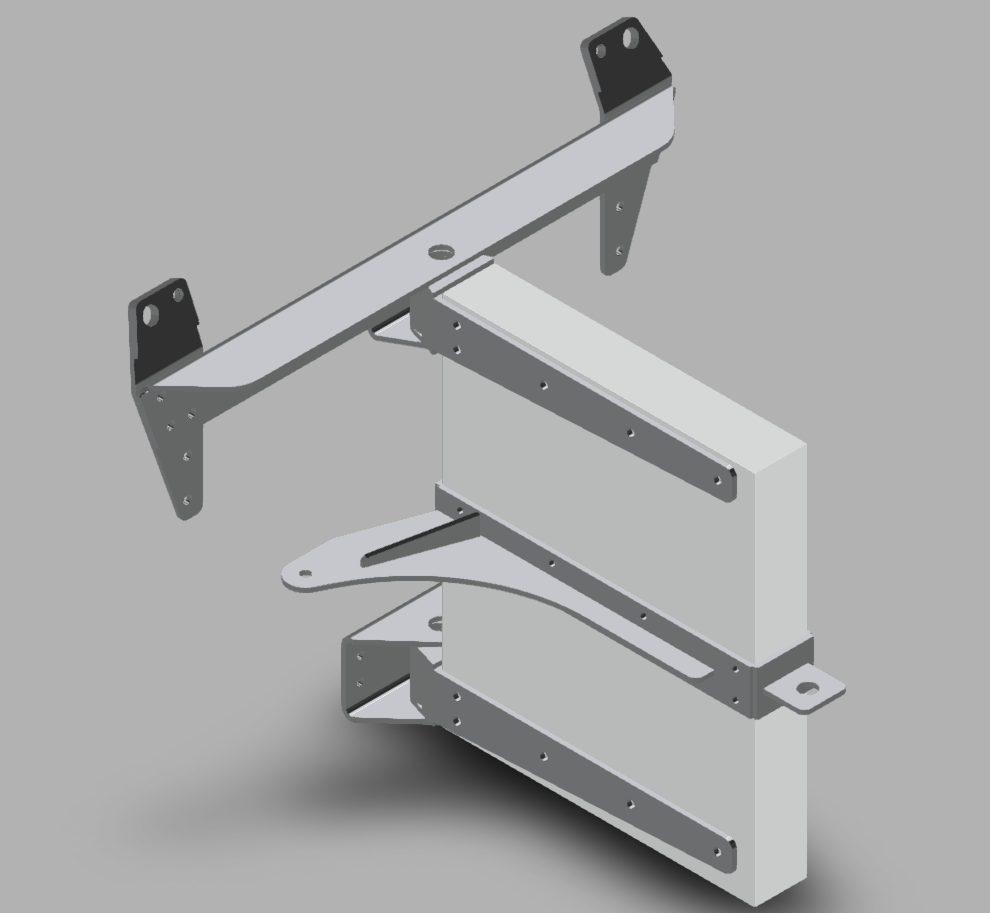
The biggest trade-off is the rudder will no longer kick up in a hard grounding. This means being a bit more careful in shallow water areas, but otherwise is a very acceptable trade-off. The aftermarket saildrive hangs down to only about one foot shallower than the rudder's depth, so beaching or grounding the boat wasn't an option in the first place.
2) Up-size the gauge of steel on the cage and pintles
The original steel was about 3mm thick. For a full cage in good condition, that might be sufficient, but it had deteriorated over the years (or was from a bad batch to start with), and failed badly.
The new mounting design uses 5mm steel for all hardware. This nets some increase in weight, but a great increase in strength.
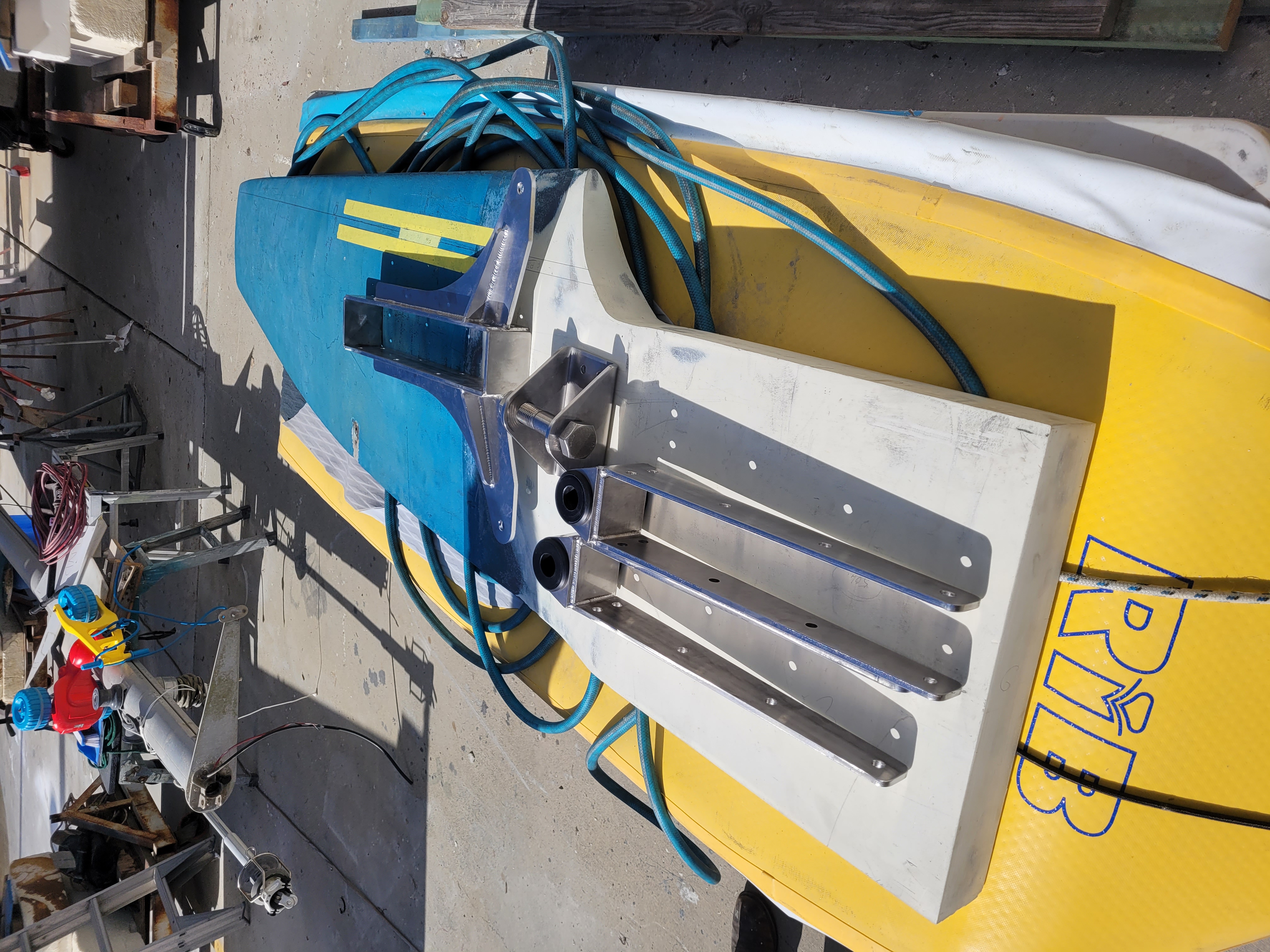
3) Increase pin-size for the attaching bolts
The pin that attached the rudder to the pintles on the stern was only about 3/4" thick, and comprised one single long pin that ran through both attachment points for the rudder. When the rudder cage failed, this pin ended up badly bent and prevented removal of the rudder to fit a backup. When the pin eventually snapped, calm conditions allowed fitting one of the spare pins aboard, but that also failed as soon as conditions got slightly rough again.
The simplicity of one large pin is nice, but the experts here identified two problems with it: first, it can (and did) fail in a way that prevents removing a damaged rudder; second, it's undersized for the amount of loads on the pin.
The new design uses a pair of 1" thick bolts, encased in high-strength plastic bearings (more on that below). These are significantly stronger, and have the advantage of being essentially "off the shelf" parts in case replacements are needed far afield. There is also no long span of pin between them that can bend or otherwise prevent removing one or the other to pull out the rudder.
4) Balance rudder mount surface area
The original design used "L-shape" brackets on the stern to which the rudder cage attached. The upper bracket had a single point of contact in an inverted-L shape, and the lower bracket had a signle point of contact in an L shape. This creates a lever arm (and thus a lot of torque load) on the stern bolts farthest from the attachment point (think: the upper part of the "L"). Thankfully, even when the rudder was dragging around broken on the stern, those bolts held, but both brackets were badly bent, and I believe other Condor 40s have had failure of those brackets over time.
The new design uses a bracket with top and bottom attachment points (think a "[" instead of an "L" shape). This removes the lever arm from the design, and, especially on the lower bracket, gives both upper and lower stern bolts a more even share of the rudder loads.
Much like the thicker steel, this nets some increase in weight, but a significant increase in strength. As importantly, it creates a more even distribution of load over the bolts on the stern.
5) Add UHMWPE bearings
The old rudder's pintle system used small metal bearings (basically, small bits of metal tube that went between the pin and the mounting bracket). These may have bound up, as the connection was steel-to-steel-to-steel, and they wore badly over time.
The new design uses ultra-high molecular weight polyethylene (UHMWPE) bearings where the stern brackets and rudder attachments are bolted together. This gives a slick, strong surface on which the rudder rotates on its pins. These bearings may wear over time, but provide greater surface area and should not bind up in the way a steel-on-steel bearing system will. The biggest downside is that these are a custom-machined part, and may be difficult to replace if needed.
6) Structural repair of rudder composites
When the original rudder was taken back to bare glass for the repairs, the team working on that discovered that a repair had been made with polyester (or vinylester) resin on top of epoxy. Due to their different chemistries, that's a weak bond, and it had failed as well. I'm not sure if this made it into part 2 (it probably should, but I think this news came after I wrote that post). That team also found unidirectional carbon fiber in the rudder which had also failed.
As a chicken-and-egg problem, it's hard to say whether the composite repair failed first, leading to the rudder cage failure; or if the rudder cage failed first, over-straining the weak composite repair, which then also failed. Either way, the composite structure had failed.
The team working on the rudder itself grinded away the failed composite until they reached good structure, and re-glassed that section in epoxy. I don't have photos of that work, but they're a highly experienced composites shop, so I'm trusting in their expertise on that.
No downsides here - just added some time and expense to the project.
While the team worked to repair the rudder, I took the damaged stern section back to bare fiberglass, so they could beef up the fiberglass there too.
In addition to those design changes, a few other steps took place. Due to the rudder damage, and the changes in design such as increasing the steel thickness and increasing the pin diameter, the top section of the rudder was slightly altered to make room for the steel hardware. This moved the rudder balance (a term in this context which means the amount of underwater rudder area that sits forward of the pivot point, which helps "lighten" the feel of the rudder when turning it) backward by about ~3%. That isn't much, but in the shakedown sailing recently it's been noticeable. It's not bad, but the rudder needs a bit more of a firm hand on it when turning, and gives a bit more "feel" than it used to.
The rudder was also repainted, re-sealed around all the new through-bolts, and re-antifouled.
And the stern brackets were re-sealed and re-attached with new hardware.
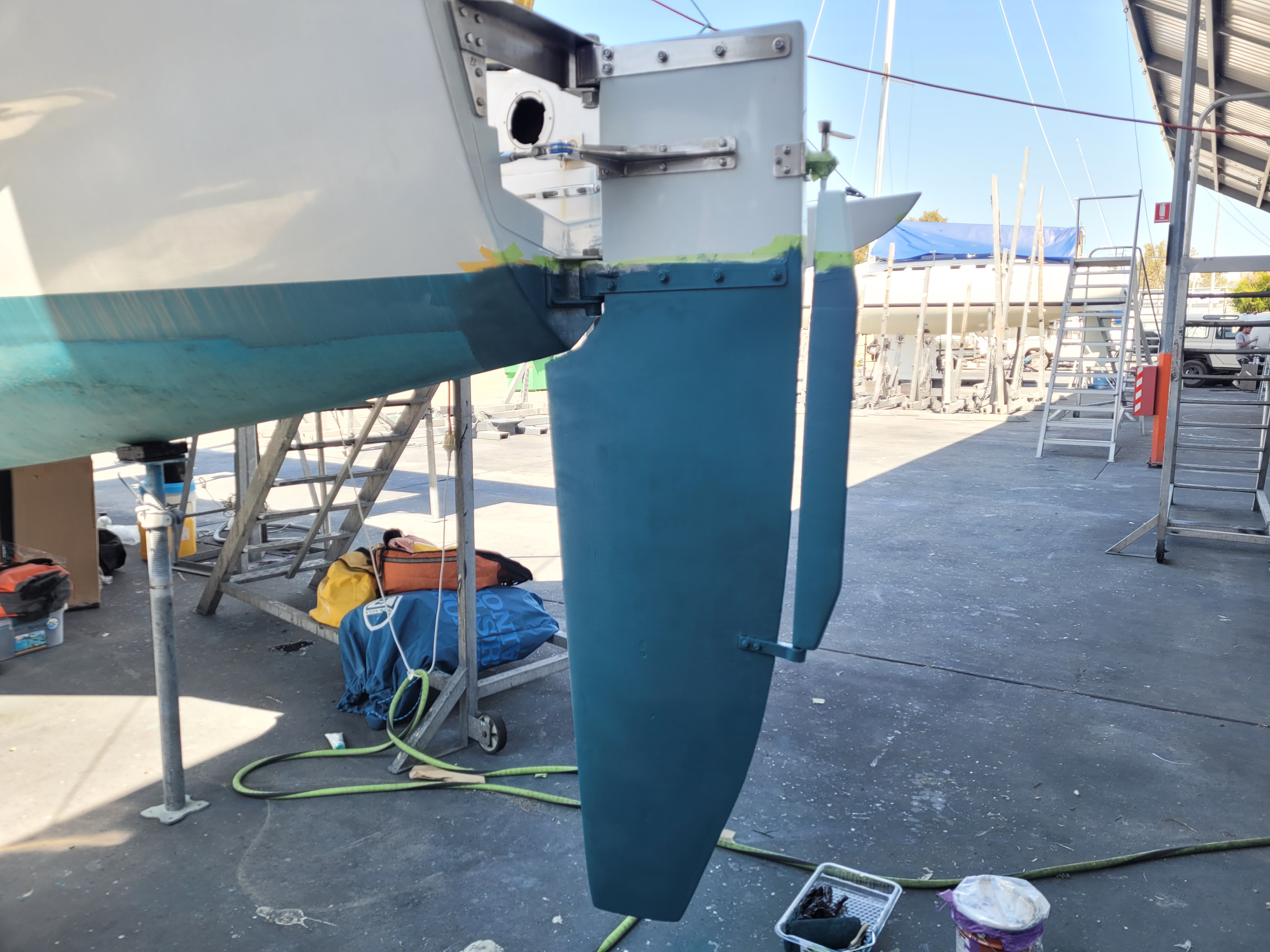
So far, it all looks good and is performing well! As of this post, the new rudder has had about a week of sailing on it, in everything from dead calm conditions to 20-25 knots upwind in steep chop. Inspection after that week has shown everything is holding up okay so far. Time's always the real test, though, and I've got a few more months of sailing before I'll stop checking it after every sail.
(2025 update: There's now over 2500 miles on the new rudder setup, and it's doing great. It held up in everything from close-hauled to dead downwind, including in some very sloppy seas. The only issue so far is the bearings seem to have developed the tiniest amount of play (~1mm) so one project next season will be to pull the rudder and inspect the components, as even that small amount of play could cause problems over time)